17. noviembre 2022 por Fernando Arévalo
Introducción a la Adquisición de Datos de Máquinas en la Planta
Encontrar patrones en los datos es una tarea que mantiene ocupados tanto a los científicos de datos como a los expertos en el área. Para las organizaciones, los datos son un activo empresarial fundamental que añade valor. Para ello, la conectividad de la planta desempeña un papel esencial.
Esta entrada del blog utiliza un ejemplo (ficticio) para explicar el papel de la conectividad en la planta.
Encontrar patrones en los datos es una tarea que mantiene ocupados a los científicos de datos y a los profesionales de proceso. A las empresas industriales les interesa porque el descubrimiento de patrones puede conducir a la optimización de los procesos (por ejemplo, identificar la mejor receta o conjunto de parámetros del proceso), a la identificación de las causas de las anomalías, a la previsión de materiales para la gestión del suministro y a la predicción del consumo energético. Por tanto, los datos son un activo empresarial fundamental que puede aportar valor. Un primer hito es la recogida de datos de la máquina.
Para ello, la conectividad de la planta desempeña un papel esencial, ya que permite acceder a los datos de las máquinas. De este modo, los datos pueden almacenarse, procesarse, analizarse y modelarse. Por último, los resultados del análisis de datos y del modelado pueden utilizarse para optimizar el proceso y crear una ventaja competitiva para la empresa.
Un ejemplo
El director de la planta volvió de la última feria industrial. Informa a su equipo: "He visto una bonita demostración de recogida de datos con máquinas en uno de los stands”. ¿Demostración en una feria? Por lo general, se trata de un caso de uso (muy) sencillo con un controlador lógico programable (PLC), algunos sensores y un bonito cuadro de mandos para mostrar variables, tendencias y algunos indicadores. El director de la planta reúne a su equipo de ingenieros. El equipo de ingenieros hace un gran trabajo para ejecutar con éxito los proyectos en la planta. ¿Tareas típicas del equipo de ingeniería? Actualización de la infraestructura eléctrica, instalación de nuevas líneas de máquinas, sustitución de componentes de automatización. El director pide un proyecto piloto en una de las máquinas para el próximo trimestre. La directora de ingeniería se rasca la cabeza, es un buen cambio en el día a día y una buena oportunidad para aprender algo nuevo, ¿no? El proyecto está definido.
La directora de ingeniería convoca a su equipo y de inmediato comienzan a hacer una lluvia de ideas. Tres o cuatro meses es poco, ¿no? El equipo da el visto bueno al proyecto. Bien, la rueda está en movimiento. Elaboran un plan y fijan los hitos clave:
- Propuesta de caso de uso (por ejemplo, definición de objetivos, medidas de éxito, presupuesto, alcance global y/o hitos).
- Evaluación de la conectividad de las máquinas (por ejemplo, tarjetas de comunicación en los PLC y el PC industrial (IPC)).
- Un diseño arquitectónico inicial para la recogida de datos (como un backend de recogida de datos ad hoc y un cuadro de mando).
- Plan de ejecución (por ejemplo, en forma de diagrama de Gantt o ágil).
Las partes interesadas están de acuerdo. Esta vez nos centraremos en la evaluación de la conectividad de las máquinas. Es un gran pastel (esto de la digitalización), un trozo a la vez por favor.
A continuación, analizamos el tema en detalle.
La conectividad del taller
El área de datos pertenece a dos mundos diferentes: Por un lado, tenemos la planta con todas las máquinas y dispositivos. Ahí es donde se crean los datos. Por otro lado, tenemos el reino de la ciencia de los datos, donde los datos añaden valor al negocio. ¡Muy bien! Eso no es todo. Tenemos otras partes, como el sistema de control de calidad, la planificación de recursos empresariales (Enterprise Resource Planning - ERP), el sistema de ejecución de fabricación (Manufacturing Execution System - MES) / el sistema de control distribuido (Distributed Control System -DCS) / el control de supervisión y adquisición de datos (Supervisory Control and Data Acquisition - SCADA). Como se ha descrito anteriormente, los científicos de datos buscan patrones en los datos. El paso más importante en este proceso es la adquisición de los datos brutos. A veces es el archivo CSV/XML proporcionado por la máquina o la consulta de un punto de datos directamente desde la máquina a través de un protocolo de comunicación. Aunque el camino hacia los datos es largo, el primer hito es asegurar la conectividad de la máquina o de la planta. Algunos de los retos más comunes que se encuentran en esta actividad son:
- La máquina no tiene tarjeta de comunicación. Aunque suene duro, esta situación significa que las máquinas no son accesibles y, por lo tanto, no hay forma de recopilar datos. Esta situación no es el caso normal, pero sigue siendo posible.
- No existe una red industrial en el taller. Al igual que en el punto anterior, no hay forma de recoger datos cuando las máquinas son sistemas isla. Por lo tanto, el equipo tiene que crear una red industrial en el taller.
- El protocolo de comunicación no es compatible con el sistema de recogida de datos. Los protocolos de comunicación industrial más comunes para la recogida de datos son OPC-UA y MQTT. Sin embargo, no todas las máquinas están equipadas con estos protocolos. La solución es actualizar la máquina con un retrofit (por ejemplo, una adaptador de MODBUS-TCP a OPC-UA).
- La máquina sólo utiliza un protocolo propio. Sin embargo, el control tiene entrada digital (DI)/salida digital (DO). El último recurso es el cableado de las señales que queremos recibir a un dispositivo intermedio (como un registrador de datos) que pueda comunicarse con el sistema de adquisición de datos.
- La máquina sólo proporciona archivos XML/CSV. Esta situación implica una carpeta compartida entre la máquina y el sistema de adquisición de datos. De este modo, el sistema de adquisición de datos puede recuperar el archivo.
Hasta aquí hemos identificado los retos comunes de la conectividad en la planta. Parece mucha información para procesar, ¿no? ¿Qué tal un diagrama general para resumir la información? El diagrama ilustra una configuración típica para la conectividad en la planta:
Trabajos preliminares para la recogida de datos de las máquinas
En esta tarea es importante tener en cuenta los siguientes puntos:
- Hay que determinar qué máquinas o sistemas (incluyendo MES, gestión de la energía) son candidatos para el sistema de recogida de datos. No hay que subestimar la cantidad de datos que puede generar una planta.
- Enumere las señales por fuente de datos y estrategia de adquisición (por ejemplo, basada en recolección periódica o por eventos).
- ¿Es necesario considerar un flujo de datos constante (data streaming)?
- La definición de una estructura de datos. Los datos estructurados facilitan la ingeniería de datos y el posterior análisis y modelado de los mismos.
- Una opción de almacenamiento de datos. ¿Deben almacenarse los datos in situ, en la nube o es necesario un sistema híbrido?
- ¿Qué pasa si las señales deseadas no están disponibles? Esta situación requiere una ingeniería adicional y adaptaciones (por ejemplo, identificación de señales, selección de sensores, programación de PLC, registradores de datos).
- Por último, pero no menos importante, los distintos sistemas de la planta deben ser accesibles al sistema de adquisición de datos. La integración del sistema desempeña un papel crucial en la selección de la plataforma de desarrollo del sistema de adquisición de datos.
Figura 1: Ejemplo de arquitectura para la recolección de datos de máquinas
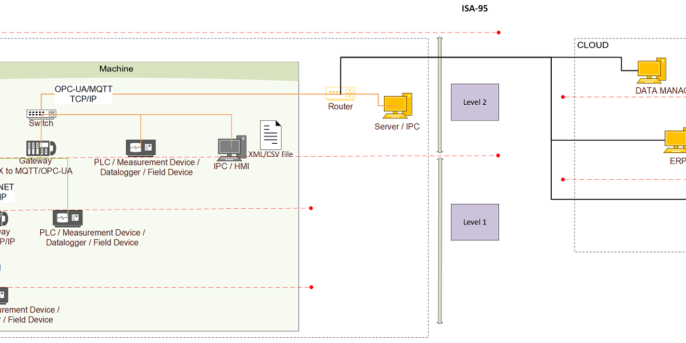
Los siguientes pasos
Se ha revisado la conectividad en la planta, así como la entrada al sistema de recolección de datos de la máquina. Los siguientes pasos incluyen el diseño del sistema de gestión de datos, la evaluación de la interconectividad de los diferentes sistemas de la planta, las consideraciones para el back-end y el front-end o el uso de una platforma de IoT establecida, qué tipo de análisis de datos se llevará a cabo, una estrategia para el mantenimiento predictivo utilizando ciencia de datos o incluso modelos de inteligencia artificial (IA) para evaluar la producción.
Nuestros expertos en IoT/IIoT, productos inteligentes, producción digital y ciencias de los datos estarán encantados de apoyarte en tus proyectos.
¿Quiere saber más sobre el IoT y nuestros servicios en este ámbito? Entonces echa un vistazo a nuestra página web o ponte en contacto con nosotros directamente.
Puede encontrar más temas apasionantes del mundo adesso en las entradas de nuestro blog (en inglés) publicadas hasta ahora.